Tideflex® Aeration Mixing Systems
Optimizing Oxygen Transfer & Mixing Characteristics
Providing optimal oxygen transfer and mixing characteristics with reliable backflow prevention, Tideflex® Aeration Mixing Systems are ideal for use in municipal and industrial aeration applications. While conventional fine and coarse bubble diffusers typically clog with sludge when airflow is interrupted due to blower shutdown or power failure, Tideflex® Aeration Mixing Systems maximize mixing while totally isolating the wastewater from the air manifold and related equipment and instrumentation.
By preventing maintenance shut downs and eliminating the need to run blowers or compressors around the clock to prevent clogging of the diffusers and manifold, Tideflex® Aeration Mixing Systems provide substantial savings in energy and operational costs.
Tideflex® Aeration Mixing Systems Design Data Form (MSWord, 236 kb)
How the Tideflex® Aeration Mixing System Works
More than 50 years ago, Red Valve developed the Tideflex® Duckbill Check Valve. This elastomer check valve allows flow in one direction only and seals closed when the external hydrostatic pressure exceeds the internal pipe pressure.
With diffused aeration systems, preventing the wastewater and biomass from entering into the air distribution system is critical to ensuring continual operation of the mixing system and the elimination of solids build-up and clogging inside the pipeline.
The Tideflex® Check Valve Air Diffuser is a proprietary compression molded Tideflex® Valve.
The two most important performance features of the Tideflex® System are 1) backflow prevention at the diffuser and 2) air discharge location within a few inches from the floor. These features allow the system to be operated in an ON/OFF blower mode for nutrient removal and also provide significant energy savings.
ON/OFF Blower Operation
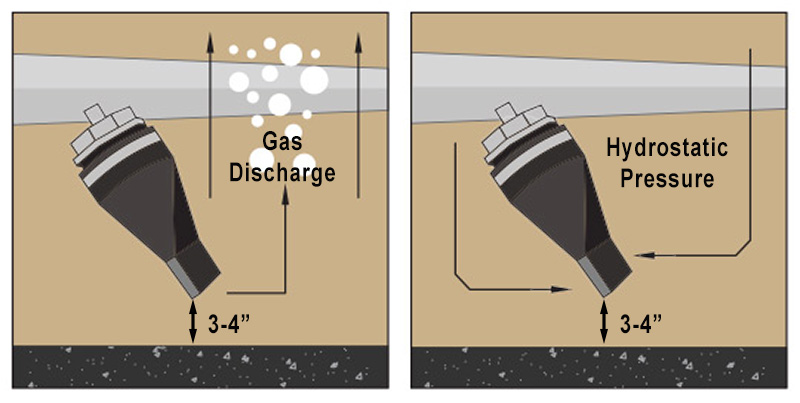
Blower ON Blower OFF
Blower ON - Gas travels vertically due to buoyancy. Fluid is educted into vertical flow path. Diffuser tip is located 3-4" (80-100mm) off the floor.
Blower OFF - Hydrostatic pressure on external sides of diffuser forces a closed seal.
Open Pore Style Diffuser Tideflex® Aeration Mixing
System
During blower operation, the Tideflex® Check Valve discharges air at near-floor elevation for complete vertical mixing. The benefit of the Tideflex® Diffuser is the prevention of sludge build-up in the bottom of the tank, eliminating backflow of the process fluid into the upstream internal pipe. Open pore style diffusers have no backflow prevention and pipes fill with sludge when the blower is off.
Biological Selector Capability
These systems can be operated as a biological selector using ON/OFF aeration and mixing. Utilizing ORP Control (Oxygen Reduction Potential), these systems can be operated at 70% less applied airflow.
High Solids Residuals Management: Aerobic Digesters & Sludge Holding Tanks
ON/OFF Blower Operational Mode
The Tideflex® Aeration Mixing System is a sealed system preventing the surrounding wastewater and solids from entering into the diffusers and manifold piping. This provides the capability to cycle the blower on and off as the process requires. For sludge storage processes, this allows for decanting and thickening of the storage residuals as well as denitrification. Most Tideflex® alternating systems reduce blower operating costs by at least 35%.
These Tideflex® Aeration Mixing Systems are preferred in high solids applications where the clogging potential is significantly increased. Wastewater treatment sludge applications range from 1% to 5% solids and water treatment alum sludge applications from 5% to 9% solids.
The Tideflex® Aeration Mixing System is the only air mixing system rated for these high solids applications, while at the same time providing maintenance-free operation.
The Tideflex® Aeration Mixing System can be applied in anoxic process zones utilizing the ON/OFF operational mode. Most anoxic zones only require periodic mixing of the bio-floc. The Tideflex® Aeration Mixing System can achieve complete mix within about one minute of operation. This short operational period results in very little oxygen transfer; these anoxic processes are in a negative ORP state where the presence of this low oxygen residual has little effect on the ORP state.
System Assembly Components
Tideflex® Aeration Mixing System Manifolds are most often constructed of all stainless steel materials. All connections are either flanged, roll grooved and coupled, or threaded. The thermal expansion couplings and rigid joint couplings are Victaulic® brand 316SS with silicone gaskets for heat control. The system piping is anchored to concrete foundations with threaded rods and Hilti® epoxy adhesives. For steel tank floors, base plates are provided for anchoring.
Channel Aeration & Mixing Systems
Channel Mixing Assemblies
Common channels in wastewater treatment facilities service multiple tanks and once put into service are impractical to drain and access equipment. These channels are susceptible to solids accumulation as the linear velocities are typically very low. The residence time in these channels can also be extended to the point where the process wastewater transitions to an anoxic state.
Channel Aeration & Mixing Systems addresses these two issues. Solids are re-suspended by the mixing loops and the residual dissolved oxygen is increased for aerobic conditions. Tideflex® Channel Aeration & Mixing Systems are designed for lift-out removal when the channels are full of water and re-insertion into the channel after inspections. The lower wall brackets act as cradles to receive and hold the horizontal distribution pipes.
The Tideflex® Channel Aeration & Mixing Systems are most often fabricated from schedule 10 stainless steel piping either 304L or 316L. The joint connections are all roll groove type using Victaulic® rigid couplings for easy field assembly. These assemblies are available in various modular lengths for the horizontal manifold section.
Wet Well Mixing
Wastewater pump station wetwells can utilize periodic mixing and oxygen supply. These modular assemblies can be applied in wet wells to break up the floatables (oil and grease) and the settled solids near the pump inlet. Often these systems are operated prior to the transfer pumps coming on-line.
Aerated Grit Tank Mixing Systems
Optimizing Existing & New Grit Tank Geometries
Aerated grit tank designs have been utilized for the last 100 years, but have never been validated in terms of performance optimization. With the availability of computerized evaluations, primarily computational fluid dynamics (CFD) programs, these older designs have been evaluated for enhancement of performance. Tideflex® has incorporated these enhancements into their Aeration Mixing System designs and recommendations, resulting in performance increases of at least 20%.
Red Valve engineers will determine the quantity of mixing zones required within the process. An evaluation should be performed for optimal operation to address storm surge capacity system needs. Grit removal systems should also provide a means for washing the biomass from the grit. This is achieved in the high-rate mixing zones at the beginning of the process. The mixing zone’s energy requirements are decreased longitudinally through the grit tank for removal of various particle diameters.
The Tideflex® Aeration Mixing System assemblies provide excellent zone mixing. Each assembly has a flow regulator valve to control the mixing loop velocity. Maintenance periods and downtime for aerated grit tanks typically result in temporary accumulation of grit within the tank, to the point where the grit blanket covers the diffusers. Plastic type diffusers fail in these loading conditions. Tideflex® Air Diffusers are extremely durable and withstand these conditions without disruption or downtime.
New Design Standards for Aerated Grit
Red Valve engineers have partnered with several consulting engineering firms in conducting CFD modeling of existing structures as well as optimized enhancements. This has allowed Red Valve to develop new design standards and guidelines for grit tank optimization. These guidelines include mixing zone quantities, energy rates, baffle locations, diffuser locations, and inlet channel configurations. Red Valve engineers provide the mixing assemblies, throttling valves, support brackets, anchors and diffuser assemblies.
Contact Red Valve engineering today for an evaluation of your existing or new aerated grit tank system for enhancement using the newest technology.
Stormwater Containment, Mixing & Aeration
Stormwater Management
Regulations for stormwater containment, testing and treatment are currently being implemented. Storage is required to capture the initial run-off and test for treatment requirements. This stormwater can contain accumulated pollutants and debris, requiring mixing systems in these storage tanks to re-suspend the accumulated solids, as well as provide residual dissolved oxygen to keep the fluid from going anaerobic.
The Tideflex® Coarse Bubble Mixing System with EPDM nozzles is very durable and can be fully exposed to weather conditions (open lagoon structures) or contained within a buried storage vault. The nozzles are non-clogging devices, making the system maintenance-free, with no need for regimented service. They are ideal for these applications that are typically located away from the primary wastewater treatment facility and its operational staff.
Tideflex® Aeration Mixing Systems can be operated in an ON/OFF mode for periodic mixing as required to significantly reduce energy usage. The check valve diffusers prevent waste and debris from entering the manifold piping and provide a maintenance-free system. The Tideflex® design models produce the most efficient configuration of piping and diffusers for optimizing controlled loop mixing and fluid momentum. Controlled loop mixing provides better mixing of heavy solids as compared to full floor coverage configurations.
Equalization Tank Mixing
Tideflex® Aeration Mixing Systems have been installed in all tank construction variations; concrete tanks, bolted steel tanks, and lined lagoons.
Equalization tank mixing systems are very similar to the design and operation of stormwater containment systems. They can be operated in a variable volume mode where the mixing system provides solids suspension and residual dissolved oxygen adequate to keep the process fluid aerobic. If an anoxic process follows to the equalization tank, then a hydraulic mixing and recirculation system should be considered. Refer to the Tideflex® HRMS Mixing System.
Highly Durable, Maintenance-Free Systems
Mixing systems are required in most storage tanks to re-suspend the accumulated solids as well as provide some residual dissolved oxygen to keep the fluid from going anaerobic. These mixing systems must be durable and dependable as they can sit idle for long periods and then require immediate operation during a storm event.
Engineering & Modeling Technology
Tideflex® Aeration Mixing Systems are designed by staff environmental and process engineers. Red Valve has developed numerous mathematical, process and hydrodynamic models for use in sizing various Aeration Mixing Systems. Red Valve continues to lead the industry in mixing technology—we welcome the opportunity to provide a no obligation evaluation of your system to help achieve optimal mixing performance.
Additional Information
Installations and Case Study Applications:
Resources Area:
Similar Type Process Systems:
U.S. Patent No. 6,016,839 / 6,193,220 / 6,372,140 / 6,702,263
Canada Patent No. 2,366,252 / 2,385,902
United Kingdom Patent No. 2,326,603